How Inertia Friction Welding Works
At Pierce Industries, we are proud to use the most innovative manufacturing processes to create custom designed parts and products for our clients.
One of the more cutting-edge techniques that we use is Inertia Friction Welding. The process is very different from traditional welding and has an incredible amount of benefits that range from being eco-friendly to being good for business. Watch this video to see IFW in action!
The Process of Inertia Friction Welding
The major difference between IFW and traditional welding is that IFW is a solid state welding process, where the material never reaches a melted liquid form. Instead, materials being welded reach a plasticized state. The process uses kinetic energy to spin one piece and then lateral force to join materials together. This is also considered a forge welding technique.
Step by Step Process
- Planning and Preparation
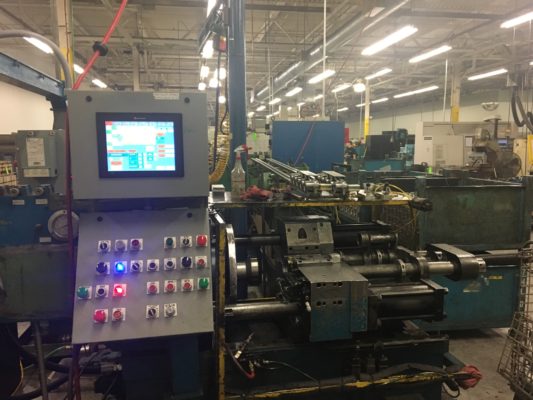
IFW is a very scientific process. Different types of metals have different qualities that give them various heat tolerances, strength, and other features. When planning a weld, the type of materials being used will determine several things: the rotational speed needed for the flywheel, and the precise amount of force needed in the lateral thrust to successfully join the two pieces.
An incredible benefit of this process is that it can actually weld dissimilar metals, where traditional welding cannot. With that, there will be different settings needed for each metal combination. Once the materials are chosen, the correct settings can be programmed into the machine. This means it is a computed weld and is easily programmable.
- Pre-Contact (Inertia)
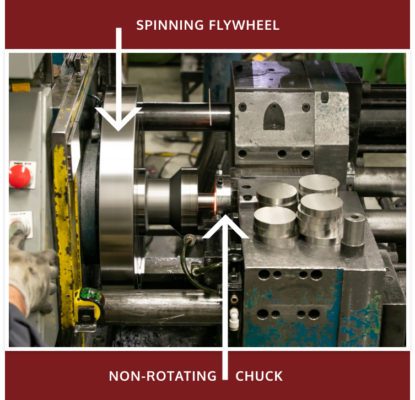
The two pieces to be welded are inserted into the appropriate receptacle. One piece will be inserted into spindle chuck with flywheel, and this is the piece which will spin. A second piece is inserted into a non-rotating chuck/fixture, which can move on a lateral hydraulic axis.
The first piece begins to spin, reaching the amount of speed pre-determined by the type of material. As the spinning reaches the top speed, the INERTIA of spinning will build up tremendous amounts of kinetic energy into the first piece.
- Contact (Friction)
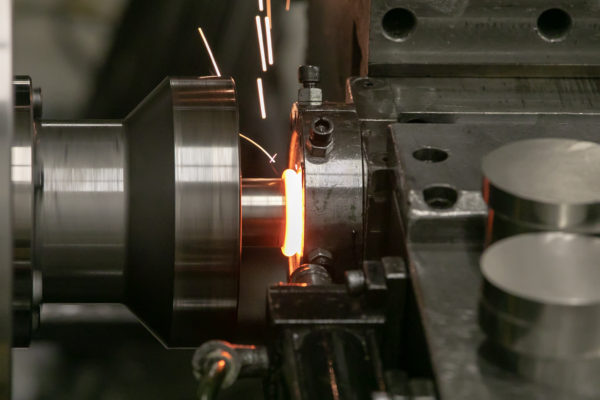
Once the flywheel has reached the predetermined speed, powered rotation stops, leaving the flywheel spinning in a freewheel state with the built-up kinetic energy. The non-rotating part is then thrust forward so the two pieces meet. This causes extreme FRICTION.
This friction then slows down the flywheel and converts all that stored up kinetic energy into frictional heat. This heat is enough to soften the metal on both pieces, but will not actually melt them into a liquid state. Instead, both pieces now have metal in a plasticized state, which means they are soft and malleable.
- Bonding
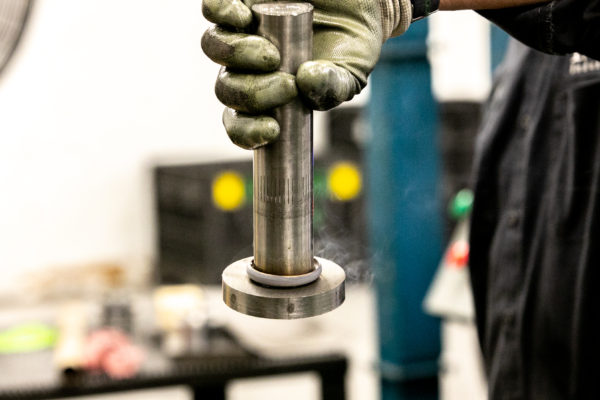
Additional thrust from the non-rotating piece will cause plastic displacement, meaning materials from each piece will flow evenly into each other, creating a full cross-sectional bond. As complex as this process sounds, the actual weld happens in a matter of seconds.
One of the more incredible aspects of IFW happens here: due to the spinning and hot-working of the metal interface, all impurities and voids are expelled.
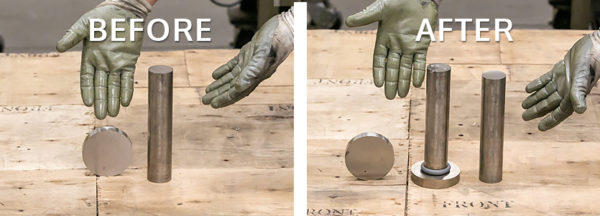
The Benefits of Inertia Friction Welding
Business Return
- Reduces cost in many ways
- Lowers material costs
- Lowers tooling costs
- Lowers Research and Development costs
- Lowers machining costs
- High-speed process means high production rates and larger quantity orders
- In turn, creates higher speed to market for final products
- Process is extremely precise and highly repeatable
- Process reduces (sometimes eliminates) the amount of scrap material
- Environmentally friendly: produces no fumes, gas, or smoke
- Speed and process combined help reduce energy consumption
Benefits of Inertia Friction Welding vs. Traditional Welding
- Can join dissimilar metals – traditional welding cannot
- Can weld a variety of pieces
- Simple to complex shapes
- Material of any finish
- Material usage is optimized: near net shapes achieved in short time
- No filler materials are necessary
- Preparation of pieces is minimal
- Variety of surfaces are weldable as is
- Spinning actions lead to self-cleaning of surfaces
- Significantly reduces the size of the heat affected zone (HAZ)
- 100% weld through the full joint interface
- Joint strength is equal or greater to that of the parent metals
- Integrity of these welds are very reliable
- Resulting joints can withstand high temperatures
Learn What Inertia Friction Welding Can Do For Your Business
There are a wide variety of applications for this exciting form of welding. We prefer to use it in the creation of custom designed rollers for our clients.
If you are curious about how we can apply Inertia Friction Welding to your latest project, or you want to request a design for custom rollers, contact us today!
Related Posts
How Pierce Industries Introduced Disruptive Technology to the Market What is Disruptive Technology? One of the more dangerous sayings in business is “but this is the way we’ve always done it.” Manufacturing and machining have been around for a long…
The manufacturing industry isn’t showing signs of slowing down. A recent look at the U.S. consumption of cutting tools shows a 10% increase year-to-date, along with an increase in machine tool orders. [Source] There are growing demands in industries that…
In the world of industrial roller manufacturing and assemblies, how do you choose the right roller for your application? When choosing or designing an industrial roller you’ll want to take into consideration requirements such as: typical speed; temperatures; load weight;…