Alternative Roller Manufacturing Design
How Pierce Industries Introduced Disruptive Technology to the Market
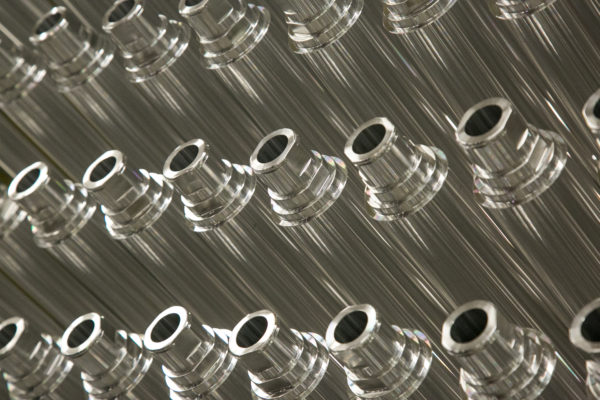
What is Disruptive Technology?
One of the more dangerous sayings in business is “but this is the way we’ve always done it.” Manufacturing and machining have been around for a long time, and businesses in the industry utilize many processes that are tried and true. Disruptive innovation comes from creating new advances which displace the current and established methods in a field.
Not only have our technological capabilities grown over the years, but in recent history, the pace of advancement has actually accelerated compared to previous decades. Innovative engineers have developed new processes that focus on two things: creating a better product and simultaneously improving the bottom line for business.
Old and Obsolete – Traditional Roller Manufacturing Process
Producing rollers for industries such as digital printing or packaging OEM’s requires the rollers to have a custom design based on the specifics of the application. A roller design typically needs two sections: the tube and the journal. A common, traditional roller design is called press fit, also known as an interference fit.
Press Fit Design
In a press fit design, three different pieces are used to create a single roller: a tube and two end caps. Press fit is an interference fit between two parts in which one is forced under pressure into a slightly smaller hole in the other.
The Drawbacks
- Cost for parts: multiple parts per roller adds up
- Extra machining: end caps require significant design and machining to reach specifications before even being inserted into the tube
- Formulas and calculations are required in order to determine the appropriate size of all pieces and the exact amount of force needed to complete the press fit
- Limited strength: sometimes requires additional adhesive or bonding to complete assembly
- Limited types of materials
- Not effective on brittle materials like die-cast metal that are used when lightweight rollers are necessary
- If end caps and the tube are made of different materials, one needs to be concerned with the CTE (coefficient of thermal expansion) of each material as this will have a direct impact on expansion and shrinkage rates in response to a change in temperature
- Bottom line: takes more time, more labor, more material, and more money
Alternative Roller Manufacturing – Cylindrical Roll Forming
Breaking away from tradition can sometimes be difficult. But when you’re faced with increasing costs for a standard product, innovative technology can give you the upper hand.
Cylindrical roll forming is time-saving, cost-effective, and manufactures an excellent end product. To produce a roller requires only one starting piece: the tube.
The Process
-
- The tube is placed in a machine which rotates the tube rapidly
- Direct heat is applied to the end, warming the material enough to be malleable
- CNC controlled mandrels shape the end into the desired neck shape
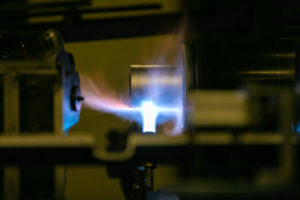
Heating the tube.
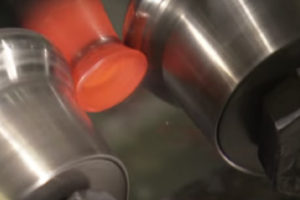
CNC mandrels forming the journals.
The Benefits
-
-
- Single piece needed: lower material cost
- Less design time required
- Produces near net shape on first run: minimal additional machining
- Can produce a wide variety of shapes
- Can completely seal the end of tube: airtight enclosure
- Works on a variety of materials: steel, stainless steel, aluminum
- Produce more than rollers: pistons, hand tools, other cylindrical components
-
Your Bottom Line
When compared to multi-piece assembly, cylindrical roll forming requires less labor and less material, which saves your business money while producing a higher quality product.
Connect with a Design Engineer
Industries that can benefit from cylindrical roll forming include digital printing, packaging, processing, glass equipment, converting, aerospace, transportation, and many more.
Contact Pierce Industries today, and we can discuss your roller needs.
Related Posts
At Pierce Industries, we are proud to use the most innovative manufacturing processes to create custom designed parts and products for our clients. One of the more cutting-edge techniques that we use is Inertia Friction Welding. The process is very…
The manufacturing industry isn’t showing signs of slowing down. A recent look at the U.S. consumption of cutting tools shows a 10% increase year-to-date, along with an increase in machine tool orders. [Source] There are growing demands in industries that…
In the world of industrial roller manufacturing and assemblies, how do you choose the right roller for your application? When choosing or designing an industrial roller you’ll want to take into consideration requirements such as: typical speed; temperatures; load weight;…